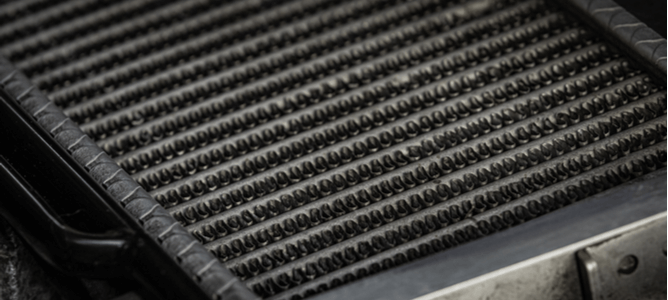
Intercoolers & Heat Exchangers: Everything You Need to Know
In many industrial manufacturing processes, excessive heat is a byproduct that must be managed to protect equipment and ensure product quality. Intercoolers and heat exchangers play crucial roles in this cooling process, but they are often mistaken for one another. The experts at NiGen will now clarify the differences between these two essential pieces of equipment and explain their specific applications.
Heat Exchanger or Intercooler?
The terms “intercooler” and “heat exchanger” are often used interchangeably, leading to confusion. We’re here to clarify the difference. Before choosing between a heat exchanger or an intercooler, it’s crucial for industrial process managers to understand how each device works.
A heat exchanger is a general term for a device that removes heat from an industrial system, enabling rapid cooling. It typically consists of tubing filled with coolant, which uses thermodynamics (the transfer of thermal energy between two contacting media) to dissipate heat from the process it’s connected to.
On the other hand, an intercooler is specifically designed to cool the air produced by an air compression unit. Commonly found in turbo-charged engines, an intercooler brings the air temperature within the compressor back to near-ambient levels before the air enters the engine. The prefix “inter” refers to its role in cooling the air between compression stages.
Heat Exchanger vs. Intercooler
Now that we’ve covered the basics, it’s clear how heat exchangers and intercoolers differ. The term “heat exchanger” is a broad category for devices that transfer heat between two substances, making them versatile across various applications. On the other hand, intercoolers are a specific type of heat exchanger designed to cool air within air compressor units.
Heat exchangers come in many forms, each tailored for different industrial cooling needs, such as:
- Shell and tube exchangers
- Boilers and evaporators
- Double-pipe heat exchangers
- Plate heat exchangers
These types of heat exchangers are important in industries like oil refining, fuel gas systems, petrochemical manufacturing, and petroleum distillation.
Important Considerations for Selecting an Intercooler
When selecting an intercooler, it’s important to consider several key factors to ensure you choose the best fit for your specific application. Here’s what to look for when picking an intercooler:
- Intercooler type (air-cooled, water-cooled)
- Anticipated system temperatures
- Size of cooling operation
- Maximum compressed air flow rate
1. Intercooler Type
Intercoolers may be air-cooled or water-cooled, depending on manufacturer design and operator preferences. While both configurations can achieve adequate cooling of compressed air, the availability of the cooling medium is a key selection criterion.
Air-cooled intercoolers can be used in virtually any environment by utilizing ambient air to pull heat out of associated processes. Water-cooled intercoolers require a steady flow of cool water to effectively achieve thermal exchange with a heated industrial process. An absence of a continuous flow of water will make a water-cooled intercooler an impractical choice.
2. Anticipated System Temperature
Each industrial application requires a unique temperature of the compressed air flowing through it. When deciding on the type of intercooler to integrate, operators must pay attention to the temperature of the air entering the exchanger and the thermal reading anticipated at the outlet after cooling. Only intercoolers able to achieve satisfactory outlet pressures should be considered.
3. Size of Cooling Operation
Intercoolers of various sizes and thermal ratings are available for cooling turbo-charged engines. Matching an appropriately sized intercooler to a cooling process is crucial to the operational efficiency and longevity of associated process components.
4. Maximum Compressed Air Flow Rate
The most effective intercooler must achieve optimal cooling at the maximum airflow rate of the compressor it is attached to. This is another crucial factor all operators must consider when choosing an intercooler device.
Lower flow rate operations might benefit from smaller-sized intercoolers. In contrast, high-flow rate processes are better served by equipment with a larger surface area that permits more rapid cooling to the desired outlet temperatures.
Intercooler Alternatives: What Are Your Options?
In operations where the integration of an intercooler is not practical, other heat exchanger units can be installed in a continuum with an air compression unit. Aftercoolers are heat exchange devices that can rapidly cool air just emerging from a compressor outlet.
This process cooling equipment has a similar setup to an intercooler with tubing filled with water, pulling heat from the compressed air (water-cooled type) or with compressed air pipes being bathed in cool ambient air (air-cooled type). This device can rapidly drop compressed air temperatures to between 5-20°F.
Get the Best Equipment for Your Industry with NiGen
At NiGen, we take pride in offering top-tier air compressors and compressed air aftercoolers to industries across the board. Our high-quality air compressor rentals are essential for industrial manufacturing, and we provide the cooling systems you need to ensure maximum efficiency. We’re committed to helping you maintain optimized productivity with reliable, state-of-the-art equipment.
For more information about our products and services or to request a quote, contact the NiGen team today! Let us partner with you to meet your industrial needs.