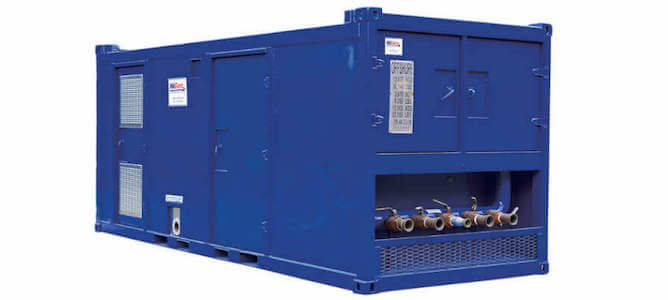
How Do Nitrogen Generators Work? – Membrane and PSA
With the numerous advantages of producing nitrogen gas on-site, many industrial users are opting for nitrogen gas generators instead of relying on cylinders delivered by vendors.
Nitrogen generators guarantee a consistent supply of high-purity gas as needed, offering safer operation and greater cost-effectiveness due to their utilization of air as the raw material. But how do nitrogen generators work? Let’s dive in.
What Is a Nitrogen Generator?
A nitrogen generator is a device that produces nitrogen gas on-site by separating it from the surrounding air. It ensures a continuous supply of high-purity nitrogen, eliminating the need for traditional cylinder delivery systems.
The vast majority of on-site nitrogen generation systems utilized in industries fall into two broad categories:
Let’s take a look at how they work:
PSA Nitrogen Generator Working Principle
The working principle of a PSA nitrogen generator is that under high pressures, nitrogen gas exhibits a strong affinity for adsorbent media such as Zeolite or Granular activated carbon (GAC). Moreover, various gases can be absorbed from a mixture at different rates, depending on the amount of pressure applied. When the pressure is lowered, the gas is desorbed.
A typical PSA generator set-up comprises two towers – one for absorption and the other for regeneration. Air coming from a compressor enters the absorption tower and contacts the adsorbent which inhibits the nitrogen gas and allows oxygen, carbon dioxide, water molecules, and impurities to pass through. To recover the absorbed N2, we simply reduce the pressure. At any given time, while the adsorption tower is separating the gas, the other is in regeneration mode.
PSA type nitrogen generators are used extensively in food and beverage packaging, electronics manufacturing, chemical industries, medical facilities, wastewater treatment plants and more to separate high-purity nitrogen gas from a compressed air stream.
Nitrogen purity using the PSA technique can be up to 99.999%, depending on the efficiency of the adsorbent and reliability of the overall system.
Membrane Nitrogen Generator Working Principle
Nitrogen membrane technology is another efficient alternative to PSA nitrogen systems. It utilizes a high-selectivity membrane for nitrogen gas separation. The material is a semi-permeable layer made of thousands of flexible, cylindrical filaments with pore sizes ranging from 0.03 to 10 microns.
To separate nitrogen gas, dry, compressed air is applied over the material which is housed in a cylindrical vessel (it is essential to use dehumidified air to prevent clogging of the membrane fibers). The membrane allows N2 to pass through but inhibits oxygen, water vapor, inert gases, and air-borne impurities. The selectivity of the membranes is highly dependent on pore size. Membrane type nitrogen generators can generate nitrogen gas with purities up to 99.95% per volume.
NiGen offers on-site nitrogen generators suitable for reliable operation in most industrial settings.
Nitrogen Generators – PSA vs. Membrane
Pressure swing absorption and membrane nitrogen generators are reliable systems capable of producing high-purity (up to 99% per volume) nitrogen gas. The main difference is in the mode of operation (PSA systems utilize adsorbents while membrane systems utilize hollow fiber membranes). Industrial users can choose from these two options based on cost considerations, quality, and efficiency.
NiGen offers both skid-mounted membrane nitrogen and PSA generation systems for industry. For short-term use, consider one of our nitrogen generator rentals.
Top 3 Benefits of On-Site Nitrogen Generators
Below are some benefits of using PSA and membrane nitrogen generators.
1. Time Savings
Generating nitrogen on-site saves industrial users from operational downtime because of nitrogen gas needs. Downtime due to logistics issues with trucking compressed nitrogen gas cylinders from vendor locations incurs huge time and financial losses for industrial users every year. In contrast, having an on-demand nitrogen generation system in place ensures that you have a 24-hour supply of high-purity gas for your processes.
2. Cost Savings
Generating nitrogen on-site proves more cost-effective than purchasing it from vendors, primarily due to savings on transportation and storage costs. This cost advantage is particularly pronounced for membrane nitrogen generators compared to PSA systems. Transporting nitrogen gas between locations necessitates the involvement of internal logistics teams or external trucking companies, which charge for freight services.
Additionally, industrial operators may need to allocate space for storage facilities on-site, subjecting their businesses to compliance with storage standards for compressed cylinders. There’s also a risk of product loss during transit, especially if temperatures fluctuate. NiGen offers high-purity on-site nitrogen generators for rent at competitive rates within the industry.
3. Safety and Reliability
On-site nitrogen gas generation systems offer enhanced safety compared to nitrogen gas from cylinders. Leaks from damaged cylinders can release toxic levels of nitrogen, especially in confined spaces. Utilizing PSA or membrane filtration systems reduces the need for cylinder storage, minimizing associated risks.
NiGen’s high-purity on-site nitrogen generators provide a reliable and cost-effective solution, ensuring uninterrupted operations and enhanced safety. Contact us today to learn more about how our nitrogen generation systems can benefit your business.
Trust NiGen for All Your Industrial Nitrogen Generation Needs
Since 1999, NiGen has been at the forefront of cutting-edge design and manufacture of on-site nitrogen generation systems. In addition to permanent sales, we offer industrial air equipment rentals to a variety of industries. Additionally, we provide field and pipeline maintenance services for industrial and O&G users.
To learn more about our services, contact our team online today!