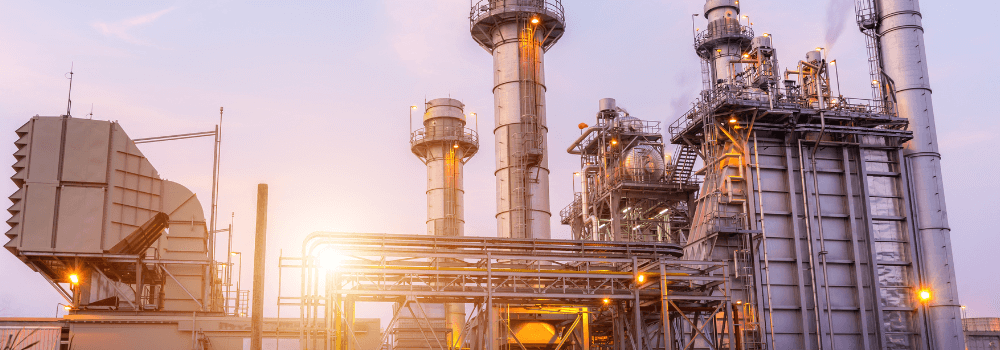
Maximizing Power Plant Operations with On-Site Nitrogen Generation
Power plants rely on nitrogen for various operations, from purging lines to preventing oxidation in sensitive components. However, a consistent nitrogen supply can be challenging and costly. On-site nitrogen generation systems solve this by providing a reliable nitrogen source directly at the power plant, boosting efficiency and reducing dependency on delivered gas.
How Power Plants Utilize On-Site Nitrogen
Power plants rely on nitrogen for processes that require a consistent, high-purity supply. On-site nitrogen generators offer plants flexibility and control, supporting critical tasks efficiently and cost-effectively. Here’s how on-site nitrogen makes a difference in power plant operations:
- Reduction in delivery, storage, and rental expenses by generating nitrogen on-site
- Constant nitrogen availability, preventing operational delays and shortages
- Fewer safety risks with reduced handling of high-pressure nitrogen cylinders
- Decreased carbon emissions from eliminating nitrogen transport and waste
- Customizable purity levels tailored to specific operational needs
1. Pipe Purging and Line Clearing
Nitrogen is essential for purging and clearing pipelines and lines, a process that removes oxygen, moisture, and contaminants to prevent oxidation and maintain equipment integrity. By creating an inert atmosphere, nitrogen helps reduce the risk of corrosion and other reactions that could degrade piping, valves, and compressors.
This is particularly useful in power plant systems that handle gases, oils, and other reactive substances. Since nitrogen purging is often a routine maintenance task, an on-site nitrogen generator ensures a reliable supply that is ready whenever needed and without dependency on delivery schedules.
Example – During shutdowns or turnarounds, nitrogen is used to purge flammable gases from pipelines, reducing the risk of combustion. This rapid, on-demand availability can minimize downtime and ensure a safe work environment during maintenance.
2. Gas Blanketing
For power plants storing or transferring combustible or reactive materials, nitrogen gas blanketing is important. By creating a non-reactive layer over stored fuels or chemicals, nitrogen gas prevents oxygen from coming into contact with the material, reducing risks of combustion or unwanted reactions.
This blanketing layer also minimizes vapor formation, lowering emissions and enhancing safety within the storage or processing facility. On-site nitrogen generation provides the continuous flow needed to maintain these blankets without interruptions, regardless of the facility’s operational demands.
Example – Gas turbines often rely on fuel storage tanks where nitrogen blanketing helps prevent fuel degradation and reduces evaporation losses, thereby maintaining fuel quality and extending storage life.
3. Cooling and Inerting
In many power plant processes, nitrogen serves as a coolant, creating an inert environment that keeps sensitive equipment free from moisture and oxygen exposure. This inerting capability is essential for turbines, alternators, and generators where even minor oxidation can impact performance and efficiency.
Large volumes of nitrogen are typically required for cooling and inerting during start-up and operational phases, especially when temperatures and pressures fluctuate. An on-site nitrogen generator can supply this demand at varying flow rates, offering flexible cooling for the unique needs of different systems.
Example – During generator maintenance, nitrogen is often used to create an inert, oxygen-free atmosphere around electrical components, preventing accidental sparking or oxidation damage during testing.
How to Implement On-Site Nitrogen Generation for Power Plants
Determine capacity requirements.
Calculate nitrogen demand based on all power plant applications, from purging pipelines to blanketing storage tanks. Select a system that handles peak loads without excessive capacity to avoid extra costs.
How much space is needed for an on-site nitrogen generator? Space requirements vary based on system capacity. For large power plants, custom setups can fit into existing infrastructure to save space and enhance accessibility.
Consider purity levels.
Different power plant applications need specific purity levels. For instance, gas blanketing might require high-purity nitrogen, while pipeline purging may allow lower purity. Tailoring purity can optimize operating costs.
Plan for redundancy.
Since nitrogen is essential to safe and efficient power plant operations, plan for redundancy by installing a backup generator or system to prevent downtime during maintenance.
Regular maintenance.
Keep nitrogen generators running smoothly with preventative maintenance, such as filter changes and leak checks. This ensures efficiency, system longevity, and minimizes risk of unexpected interruptions.
Nitrogen generators are relatively low-maintenance, especially when compared to the logistical coordination required for delivered nitrogen. Regular, straightforward maintenance like filter changes and system checks ensure efficient operation.
What is the expected ROI for on-site nitrogen generation?
ROI depends on the specific nitrogen needs of the plant and the cost of delivered nitrogen. However, most plants see a positive return within 3 to 5 years due to reduced operating costs.
Improve Your Operations with On-Site Nitrogen
Looking for a trusted nitrogen generator manufacturer in Houston? At NiGen, we’re all about helping power plants run smoother, safer, and more cost-effectively. With our on-site nitrogen generation systems, you eliminate downtime waiting for nitrogen deliveries, reduce costs, and gain more control over your nitrogen supply. Our team of specialists is always ready to help you find the ideal system for your facility.