
Troubleshooting Your Air Compressor: A Step-by-Step Guide
Like most equipment, industrial air compressors can experience issues that affect performance. As a professional with years of experience in air compressor systems, I’ve put together this step-by-step air compressor troubleshooting guide to help you with common problems.
Step 1: Identify the Problem
Before jumping into air compressor repairs, take some time to identify the issue clearly. Air compressors can exhibit various symptoms depending on the problem. Here are some common issues to look for:
- Lack of Air Pressure: The system isn’t producing enough air to operate tools or machinery.
- Excessive Noise: A loud or unusual sound is coming from the compressor.
- Compressor Won’t Start: The motor is not kicking on.
- Frequent Cycling: The compressor turns on and off too often.
- Air Leaks: You notice air escaping from hoses or fittings.
Knowing what you’re dealing with helps narrow down the cause, so take note of these symptoms before continuing.
Step 2: Check the Power Supply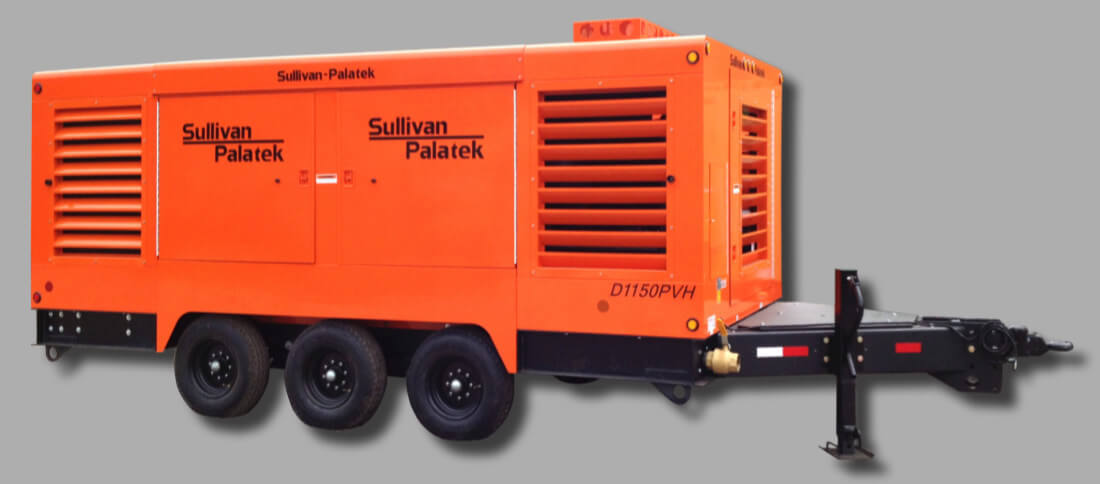
A common and easily overlooked problem is the power supply. If your compressor won’t start or operates intermittently, it might be a power issue. Here’s how to check:
- Power Switch: Ensure the power switch is on and functioning.
- Circuit Breaker: Check the breaker to see if it has tripped.
- Power Cable: Inspect the power cable for any visible damage.
- Voltage: Verify that the correct voltage is being supplied to the unit.
If you find any issues with the power supply, they should be fixed before continuing with further air compressor troubleshooting.
Step 3: Examine the Air Filter
Air filters can get clogged with dirt, dust, and other contaminants, which can reduce airflow and lead to inefficient operation. A dirty air filter can cause the compressor to work harder, raising energy consumption and shortening its lifespan.
- Location: The air filter is typically located at the intake of the compressor.
- Inspection: Remove the filter and inspect it for dirt buildup or damage.
- Cleaning/Replacement: Clean the filter if it’s washable, or replace it if it’s too dirty or damaged.
Step 4: Inspect the Pressure Switch
The pressure switch controls the compressor’s operation by turning it on or off based on air pressure levels. If the compressor is cycling on and off too frequently, or if it won’t start at all, a malfunctioning pressure switch could be the culprit.
- Check for Proper Setting: Make sure the pressure switch is set to the correct pressure range.
- Inspect for Damage: Look for signs of damage or wear, such as leaks or cracks in the housing.
- Testing: If the switch appears damaged or faulty, it may need to be replaced.
Read Now: INDUSTRIAL AIR COMPRESSOR SAFETY GUIDE
Step 5: Check for Leaks
Leaks in your air compressor system can cause a drop in pressure and lead to inefficient operation. They can occur at fittings, hoses, or valves. If you notice a decrease in pressure, follow these steps:
- Visual Inspection: Check all hoses and connections for visible signs of wear, cracks, or loose fittings.
- Soapy Water Test: Apply soapy water to connections and look for bubbles that indicate a leak.
- Tighten Fittings: If a leak is found, tighten the fitting or replace the hose.
Step 6: Look at the Oil Levels and Quality (for oil-lubricated compressors)
For oil-lubricated compressors, oil levels and quality are critical to smooth operation. If your compressor is making excessive noise or isn’t performing as expected, it might need oil maintenance.
- Check Oil Level: Make sure the oil level is within the recommended range.
- Oil Quality: If the oil looks dirty or contaminated, replace it with fresh oil to prevent damage to the moving parts.
- Oil Filter: If your system has an oil filter, inspect and replace it if necessary.
Step 7: Examine the Cooling System
Overheating can cause compressors to shut down or malfunction. Cooling systems are designed to prevent this. Here’s how to inspect it:
- Airflow Blockages: Check for any blockages around the cooling fan or ventilation areas.
- Temperature Regulation: Ensure the compressor is operating at the correct temperature by checking the gauges.
- Compressor Location: If the compressor is in an enclosed space, ensure there’s adequate ventilation to prevent overheating.
Step 8: Inspect the Unloader Valve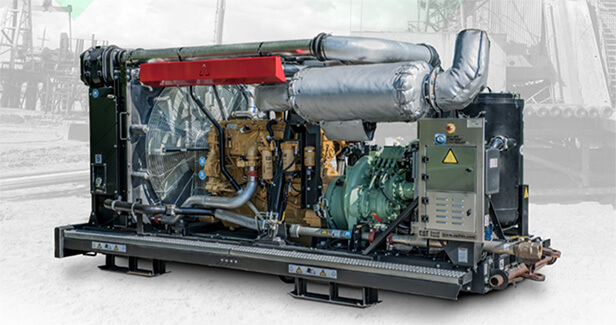
The unloader valve releases excess pressure when the compressor cycles off, preventing damage to the system. If the unloader valve isn’t working correctly, the compressor could struggle to start or stop correctly.
- Check for Malfunctions: Make sure the valve is functioning properly and releasing pressure when it should.
- Inspect for Blockages: Clean any debris or buildup from the valve to ensure smooth operation.
Step 9: Review the Compressor’s Maintenance Schedule
Regular maintenance is key to extending the life of your compressor and preventing issues before they happen. If you haven’t been keeping up with your compressor’s maintenance schedule, it’s time to catch up.
- Check the User Manual: Refer to the manufacturer’s guidelines for air compressor maintenance intervals and procedures.
- Scheduled Inspections: Regularly check filters, belts, and other parts for wear and tear.
- Routine Oil Changes: If your compressor uses oil, be sure to change it on schedule.
Read Now: SIGNS IT’S TIME FOR AN AIR COMPRESSOR AUDIT
Step 10: When to Call a Professional
If you’ve gone through all the air compressor troubleshooting steps and your unit still isn’t functioning properly, it might be time to call in a professional. Complex issues, like electrical malfunctions or internal damage, are best handled by a technician.
Need help with air compressor troubleshooting or upgrading your system? At NiGen, we provide industrial-grade air compressors, aftercoolers, and nitrogen generators to optimize your operations.
Contact us today for expert advice and air compressor rentals!