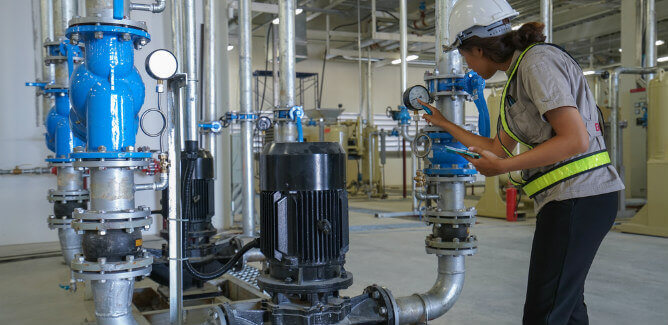
Danger of Moisture in Compressed Air Lines & Processes
Regardless of whether an industrial manufacturing process generates or consumes thermal energy, there is a high likelihood of moisture accumulation. This is particularly worse for industrial systems that circulate environmental air.
Depending on the environment, ambient air contains varying amounts of water vapor suspended alongside its other elemental components. While a bit of moisture should be anticipated in circulating process systems, if ignored the implications can be costly in terms of maintenance and machinery downtime which will hamper optimal productivity.
This article will define the dangers associated with the presence of water vapor within compressed air systems and suggest effective ways to conduct air compressor moisture removal.
Damaging Effects of Moisture in Compressed Air
There are various undesirable implications of having moisture circulating within a compressed air system. Outlined below are common problems anticipated with the presence of significant vaporized water in compressed air pipelines.
Increased Risk of Corrosion
An increased level of water in air lines is an ominous sign for the dynamic parts of process systems. Water in compressor lines will wash away machinery lubricants and speed up the rate at which metal parts rust.
These undesirable effects of retained moisture will translate into a higher total cost of maintenance as compressor parts will require replacement more often than usual.
Damage to Pneumatic Control Systems
Various industrial processes incorporate pneumatic control systems that regulate critical production equipment. The presence of high levels of moisture within these air regulated systems will significantly reduce productivity as malfunction controls will lead to costly maintenance downtime.
Plant Air Contamination and Diminished Production Efficiency
Most industrial manufacturing processes require moisture-free, compressed air to properly function. The presence of vaporized water in compressed air lines will speed up the onset of corrosion which may then clog the circulating tubing and reduce process efficiency.
Additionally, suspended water vapor will shorten the half-life of sensitive apparatus necessitating repeated and costly replacements.
Damage to Cylinder and Valve Systems
Condensation in a compressed air reservoir will cause the accumulation of debris within the air system circulation. This water will coalesce with other solid impurities like dirt and oils and damage the processes.
These mixtures can narrow airflow tracts and dry lubrication on machinery parts slowing down production speeds. Further, compressed air contamination can damage rubber components of equipment valves causing them to stiffen or even rupture.
Alterations in the Quality of Finished Products
In the food manufacturing industry, the presence of condensation in an air compressor system has dire consequences. When functioning properly, pneumatic compression systems are employed to dry the packaging for perishable foods. If moisture impurities from the compressed air enter the packed food items, there will be a significant alteration in the quality and shelf life of the finished items.
How to Get Water Out of Air Compressor Lines
Air compressor water removal can be conducted using various methods. Most of the water elimination techniques routinely employed depend on several factors which include:
- Compressed air dew point requirements
- The temperature of the ambient air
- Air compression pressure ratings
- The unique requirements of the associated process
- Airflow dynamics
After carefully considering the above criteria, an industrial operator should be able to decide the water removal technique best suited to a unique production process. The most effective methods employed to remove moisture from compressed air are outlined below.
Compressor Tank Drainage
Air compressor tanks have a release valve at their base which helps release accumulated water from within the compressed air circuit. If routinely done, releasing water from compressed air systems help to maintain humidity levels within acceptable ranges. Automatic water drains can be installed as add-ons to remove accumulated water at scheduled intervals.
Water Trapping Systems
Water traps can be installed into air compression systems which will help eliminate a significant amount of moisture from processes that require dry air for optimal operation.
Air Dryers
While filters and water traps can eliminate most of the water vapor in compressed air, the most efficient means of moisture removal is using air dryers. Instrument air dryers can be refrigerated air dryers or desiccant type dryers.
Refrigerated Air Drying Systems
These types of dryers function similarly to air conditioners. Compressed air is passed through the dryer which cools it to low temperature at which the suspended water condenses and can be collected separately. Refrigerated systems efficiently dry compressed air making them suitable for moisture-sensitive industrial processes.
Desiccant Air Drying Systems
Air desiccant dryers (which may also be referred to as absorption dryers) are composed of hygroscopic materials typically housed within drying towers. When air is passed over these absorbent substances, they retain moisture while the dried air can flow out to associate industrial processes.
Most standard desiccant drying systems are regenerative types with two towers. While one tower is actively drying compressed air, saturated desiccant in the other tower is being regenerated for the next cycle of drying.
NiGen offers cost-effective air dryer rentals for your industrial needs. Request a quote today!
NiGen Can Protect Your Process Air Equipment
For nearly two decades, NiGen has been providing cutting edge air drying solutions suited to various industrial process needs. Our high quality desiccant dryers and industrial air compressor rentals can help serve all your process air requirements.
Contact the NiGen team online today for more information about our products and services.