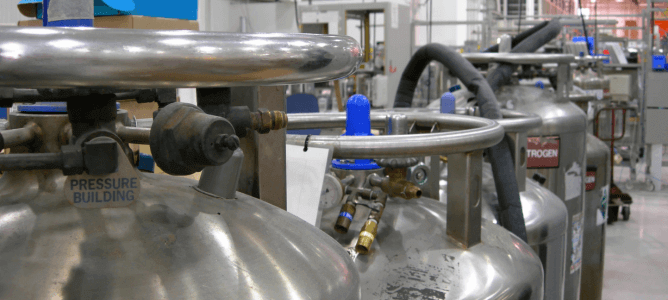
On-site Nitrogen Generator Safety Guidelines
Nitrogen is a widely used industrial gas critical in various sectors, including electronics, food packaging, and pharmaceuticals. While nitrogen is inert and non-toxic, its handling and generation pose risks, which makes awareness of nitrogen generator safety crucial.
Understanding the Dangers of Handling Nitrogen
Nitrogen gas safety is a critical aspect that is often overshadowed by the non-reactive nature of nitrogen. It’s crucial to understand the following risks to ensure safety in handling nitrogen:
- Asphyxiation Risk: When nitrogen gas leaks in a confined space, it can rapidly reduce the oxygen concentration. Human beings require a certain level of oxygen in the air to respirate, and a drop below this level can lead to unconsciousness or even death.
- Explosion Hazard: When liquid nitrogen is vaporized and trapped in a sealed container, it can lead to explosions due to rapid expansion. As liquid nitrogen converts to gas, it expands up to 694 times its liquid volume.
- Cold Burns and Frostbite: Contact with liquid nitrogen can cause cold burns or frostbite. Due to its extremely low temperature, it can freeze skin and eye tissue on contact, resulting in serious injury.
- Pressure build-up and Container rupture: Improperly vented containers lead to pressure build-up as liquid nitrogen evaporates, potentially causing container rupture or explosion.
On-Site Nitrogen Generators Are the Safest Way to Supply Nitrogen
On-site nitrogen generators use either PSA or membrane technology to extract nitrogen from the air. The ambient air, which contains about 78% nitrogen, is compressed and passed through a filtration system. In PSA systems, the compressed air cycles through adsorbent material beds which selectively absorb oxygen, allowing nitrogen to pass through. In Membrane systems, gasses in the air are separated based on molecular size and diffusivity through a semipermeable membrane, resulting in high-purity nitrogen.
Safety Advantages of On-site Nitrogen Generation
Reduced Handling Risks
Conventional nitrogen supply often involves the handling and transportation of high-pressure cylinders or cryogenic liquids, which pose risks of explosions or asphyxiation. On-site generators eliminate the need for such handling, reducing the risk of accidents.
Constant Supply at Safe Pressure
These systems provide a continuous flow of nitrogen at safe, regulated pressures. This continuous supply minimizes the risk of pressure fluctuations or sudden release incidents.
No Storage of Hazardous Materials
Storing large volumes of compressed gas or cryogenic liquid nitrogen can be hazardous. On-site generators produce nitrogen as needed, reducing the risks associated with storage.
Control Over Purity Levels
Users can control the purity level of nitrogen, which is critical for safety in applications where specific purity levels are required to avoid chemical reactions or explosions.
How On-Site Nitrogen Generators Enhance Safety
On-site systems operate at much lower pressures than cylinder gas, significantly reducing the risk of explosive decompression and leaks. The purity level of nitrogen can be precisely controlled, ensuring safety in processes where specific purity levels are critical.
On-site nitrogen generators also provide monitoring systems that can detect leaks, pressure drops, or purity issues, and alert operators to potential safety issues. These generators can be designed to meet the specific requirements of a facility, including size, flow rate, and purity, ensuring a safe fit for the intended application.
By performing nitrogen generator maintenance and safety checks, these systems can be maintained by on-site personnel. This allows for regular safety checks and immediate attention to any issues, which is not as feasible with delivered nitrogen.
Key Safety Guidelines for Nitrogen Generation Operations
To prevent accidents and ensure personnel safety when using on-site nitrogen generators, operators should adopt the following detailed guidelines:
- Ensure Proper Ventilation and Air Monitoring: Adequate ventilation is essential in areas where nitrogen generators operate. This ensures that any leaked nitrogen gets quickly dissipated, reducing the risk of oxygen displacement. Regular monitoring of oxygen levels in these areas is crucial. Install oxygen deficiency monitors that trigger alarms if oxygen levels fall below safe thresholds.
- Perform Regular Maintenance and Inspections: Nitrogen generation systems should be regularly inspected and maintained according to the manufacturer’s specifications. This includes checking for leaks, ensuring filters and membranes are clean and functional, and confirming that control systems are operating correctly. Preventative maintenance not only prolongs the life of the equipment but also reduces the risk of accidents.
- Ensure Leak Detection with Timely Repairs: Since nitrogen is colorless and odorless, detecting leaks can be challenging. Use appropriate leak detection methods, such as ultrasonic detectors, to identify leaks. Any identified leaks should be repaired immediately to prevent the accumulation of nitrogen in enclosed spaces.
- Use Personal Protective Equipment (PPE): Operators should wear appropriate PPE, such as gloves and safety glasses. In environments with a potential risk of oxygen deficiency, it might also be necessary to use oxygen monitors and breathing apparatus.
Read Now: Is It Time to Upgrade Your Nitrogen Equipment?
Additional Safety Considerations
Safe Storage and Handling of Generated Nitrogen
If nitrogen is stored in cylinders or tanks after generation, ensure these containers are appropriately rated for the pressure of the stored gas. Follow standard practices for the handling and storage of compressed gases.
Design and Installation Standards
Ensure that nitrogen generators are designed, installed, and tested in accordance with relevant standards and guidelines. This includes proper sizing, selection of materials compatible with nitrogen, and adequate safety controls.
Use Pressure Control and Relief Systems
Include proper pressure control and relief systems to prevent over-pressurization in the nitrogen generator and storage systems. Regularly inspect and test these systems.
Emergency Shut-off Systems
Implement emergency shut-off systems that can quickly stop the generation process in case of a malfunction or emergency.
Read Now: Nitrogen Generator Troubleshooting Guide
Invest in Nitrogen Generation Solutions from NiGen for Safe Operations
NiGen offers state-of-the-art nitrogen generation solutions that prioritize safety and efficiency. When you choose NiGen, you can benefit from advanced technology tailored to meet specific requirements while adhering to the highest standards of nitrogen generator safety.