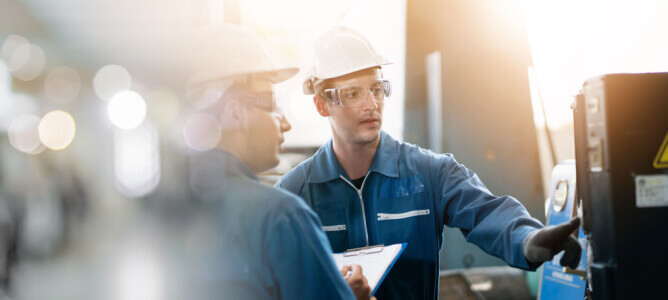
Air Compressor Installation 101: A Step-by-Step Guide
Installing anindustrial air compressor sets the stage for reliable, efficient performance throughout a facility. It involves careful consideration of airflow demand, system configuration, ambient environment, and how the unit ties into existing operations. At NiGen, we approach installation as a key part of the compressed air system’s lifecycle – something that influences pressure stability, energy use, and long-term maintenance needs. A well-executed setup ensures the compressor delivers as intended from day one.
Pre-Installation Checklist
Before you start the air compressor installation process, make sure you’ve covered the basics. You have to make sure your setup supports long-term performance and efficiency. Here’s a quick checklist to help you get started on the right foot:
-
Determine Air Demand (CFM): Calculate the total air consumption required by your tools and equipment to ensure the compressor can keep up with demand without short cycling or excessive wear.
-
Select the Right Compressor Type: Choose between rotary screw, reciprocating, centrifugal, or other types based on your usage patterns and application. Not every job needs the same style of compressor.
-
Check Power Availability: Confirm that your electrical system can support the voltage, phase, and amperage required by the compressor. Most industrial models need a dedicated power supply.
-
Evaluate Ambient Conditions: Make sure the installation area stays within the manufacturer’s recommended temperature and humidity range. Excess heat or moisture can damage the equipment or shorten its lifespan.
-
Plan for Access and Clearance: Leave enough space around the compressor for proper airflow, heat dissipation, and routine maintenance. Tight installations make service more difficult and increase operating temperatures.
At NiGen, we emphasize this phase to make sure every part of the environment is aligned with the compressor’s requirements. A structured checklist not only reduces the risk of delays during commissioning but also lays the groundwork for smooth, uninterrupted operation.
How to Install an Industrial Air Compressor
Proper air compressor installation is key to ensuring your air compressor operates efficiently, safely, and within manufacturer specifications. Let’s walk through the steps to get it set up correctly.
Step 1: Choose the Right Location
The first step in installing an air compressor is selecting the correct placement. Consider factors such as noise levels, ventilation, accessibility, and proximity to electrical outlets. You’ll want to choose a well-ventilated area with enough space for the compressor and easy access for air compressor repairs and maintenance.
Step 2: Prepare the Foundation
Before installing the air compressor, ensure that the foundation is level, stable, and capable of supporting the weight of the equipment. A concrete pad or a sturdy floor is ideal for this purpose. If necessary, use shims or leveling tools to achieve a stable base.
Neglecting proper foundation preparation can result in adverse consequences: increased vibrations and noise, misalignment issues, reduced air compressor lifespan, safety hazards for personnel, higher maintenance costs, and overall degradation in compressor performance.
Step 3: Connect the Power Supply
Next, connect the air compressor to a suitable power supply. Follow the manufacturer’s instructions and local electrical codes to ensure proper wiring and grounding. Use a dedicated circuit with the correct voltage and amperage rating to avoid overloading the electrical system.
Step 4: Install the Air Intake Filter
Proper air filtration is crucial for the longevity and efficiency of your air compressor. Install an air intake filter to prevent dust, debris, and contaminants from entering the compressor. Ensure that the filter is easily accessible for regular cleaning or replacement.
Failing to properly install the air intake filter can lead to severe consequences. Without proper filtration, airborne contaminants such as dust and debris may enter the compressor, causing increased wear on internal components, reduced efficiency, potential damage to the compressor elements, and compromised air quality in downstream applications.
Step 5: Set Up the Pressure Regulator and Safety Valve
Install a pressure regulator to control output and a safety valve to prevent over-pressurization. Both components must match the compressed air system’s pressure requirements.
NiGen tip: We always bench-test safety valves prior to air compressor installation. It adds a few minutes but could prevent a costly failure.
Step 6: Connect the Air Outlet
To use the compressed air, connect an air hose or piping system to the compressor’s outlet. Use high-quality fittings and connectors that are compatible with your specific air tool requirements. Ensure that all connections are tightened securely to prevent air leaks.
Improperly connecting an air hose or piping system to the compressor’s outlet can be detrimental. Air leaks may occur, leading to reduced system efficiency, increased energy consumption, and potential damage to the air compressor due to overheating. Insufficient connections can compromise the overall integrity of the compressed air system, impacting downstream applications and potentially causing safety hazards.
Step 7: Test and Adjust
Power up the compressor and allow it to build pressure. Listen for unusual noises, check for leaks, and verify system response. Adjust the pressure regulator to meet your operational needs.
NiGen tip: Log the baseline performance – pressure build-up time, amp draw, and decibel levels. It gives you a benchmark for future diagnostics. Learn more about air compressor testing.
Step 8: Regular Maintenance
To keep your new air compressor running smoothly, perform regular maintenance tasks such as checking and replacing filters, draining condensate from the tank, and lubricating moving parts. Refer to the manufacturer’s guidelines for specific air compressor maintenance instructions and intervals.
REMEMBER: Proper air compressor installation and air compressor audits are essential for the safe and efficient operation of your compressed air system. Always consult the manufacturer’s instructions and seek professional assistance if needed. Following these steps, you can enjoy the benefits of a reliable air supply for your various projects and applications.
Get Started with NiGen’s Industrial Air Compressors
Ready to get started? NiGen also offers nitrogen generators, air dryers, booster compressors, and full pipeline service solutions. From air compressor installation and rentals to on-site support, our team is here to keep your operation running at peak efficiency.
Get in touch with our team to learn more about the various types of air compressors we have available for purchase and rent, or if you have more questions about air compressor installation!